Si può migliorare la stampa di oggetti con difficili sottosquadra? Forse si.
Ecco una breve descrizione della D3, la stampante che permette di variare l’angolo di uscita della plastica dall’estrusore, rispetto alla direzione della gravità, durante la stampa di un oggetto.
Questa stampante è stata presentata per la prima volta alla Maker Faire 2015 a Roma e fa parte del materiale a disposizione dei maker che portano avanti i loro progetti al SciFabLab.
Prime idee
Uno dei più grandi nemici della stampa 3D è la gravità: infatti quando la plastica viene fusa dall’estrusore non può far altro che cadere verso il basso.
Per questo inizialmente ho pensato che ruotando la stampante di 180 gradi fosse possibile ottenere dei risultati migliori su alcune superfici con sottosquadra particolarmente difficili.
I primi test sono risultati molto incoraggianti in quanto si notava un netto miglioramento nella stampa di oggetti attaccati al piano da punte molto sottili.
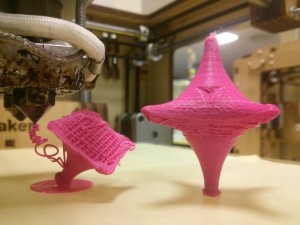
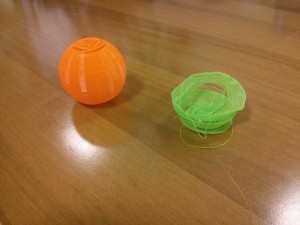
Sviluppo della stampante al contrario
Convinto da questi risultati ho cominciato la progettazione di un supporto che permettesse la rotazione della stampante lungo l’asse y, in modo da porterla ruotare la stampante agevolmente.
Per questo progetto ho scelto di utilizzare una Ultimaker Original, uno dei modelli di stampante commerciale più diffusi, e di studiare una struttura che potesse essere costruita in qualsiasi Fablab dotato di tagliatrice laser, evitando di utilizzare viti o chiodi e non modificando in alcun modo la stampante stessa.
Per la costruzione ho utilizzato il legno tagliato con la lasercutter, ma è risultato chiaro fin dal primo prototipo che il movimento degli ingranaggi era fortemente ostacolato dall’attrito dovuto al peso della stampante.
C’era inoltre un altro problema: la struttura costruita in questo modo era difficilmente motorizzabile e quindi non controllabile con uno stepper.
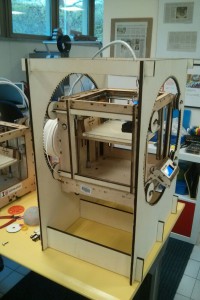
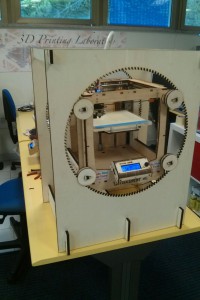
La svolta e la nuova teoria
A questo punto era chiaro che c’era bisogno di un disegno totalmente diverso da quello sviluppato fino a questo momento: la struttura doveva essere portata sulla stampante e lo stepper doveva essere fissato sulla base, in modo da controllare il movimento dell’intera struttura.
Mi resi anche conto che in questo modo avrei potuto avere l’intero controllo sul movimento durante la stampa e quindi la possibilità di ruotarla anche di 90 gradi per poter fare i \”ponti\”, uno dei maggiori problemi della stampa 3D. Ma perchè fermarmi a questo punto?
Come detto prima il problema della stampa 3D è la gravità stessa: quando la plastica esce fusa dall’estrusore non può far altro che seguire la gravità verso il basso.
In realtà abbiamo anche un altro componente sempre perpendicolare al piano di stampa, cioè la pressione con cui esce dall’estrusore. Tuttavia imponendo una condizione di stampa a bassa velocità, nella quale possiamo trascurare la pressione di uscita della plastica dall’estrusore, l’unica forza agente sulla plastica è la gravità.
Quindi non ci resta che sfruttare la gravità a nostro favore: mantenendo il piano tangente alla superficie del solido che vogliamo ottenere ad un angolo di almeno 45 gradi rispetto alla base di stampa, angolo ottimale per ottenere dei buoni risultati, la gravità influirà in modo marginale sulla stampa, permettendoci di sfruttare nuove modalità di slicing.
Sviluppo del quarto asse
Ritornado alla stampante e applicando quanto detto risulta chiaro che il progetto ha preso una piega totalmente diversa.
Ora la struttura deve:
- essere costruibile in un Fablab;
- senza chiodi ne viti;
- senza modifiche ne strutturali ne firmware alla stampante;
- ruotabile durante la stampa.
Su consiglio di Carlo, smetto di disegnare ingranaggi su sui far scorrere la stampante e mi concentro su una struttura, da fissare alla stampante, liscia e circolare, che andrà a scorrere in dei cuscinetti sulla base fissa appoggiata al tavolo. Sul lato interno della parte fissata sulla stampante è stata intagliata una corona su cui scorrerà l’ingranaggio fissato allo stepper.
Per quanto riguarda il fissaggio dello stepper alla base ho deciso di utilizzare il peso stesso dello stepper per dare la giusta tensione all’ingranaggio: infatti il pannello che sostiene il motore è libero di muoversi in verticale e solo il peso lo mantiene della sua posizione.
Questa soluzione ha anche un altro vantaggio: se il sistema improvvisamente ha un problema posso sganciare il motore dalla corona semplicemente sollevandolo.
I cuscinetti, per evitare viti e per poter esser completamente costruibili in un Fablab (per non parlare dell’estetica =) ), sono stati sostituiti cuscinetti planetari modificati ed ingranditi, fissati con una serie di perni ed incastri.
Sviluppo software
Costruito e montato il tutto sono passato alla parte software. L’Ultimaker Original permette l’utilizzo di solo 5 motori, 3 assi e 2 estrusori; questo implica che lo stepper che andrà a muovere questo nuovo asse della stampante dovrà per forza essere quello del secondo estrusore.
Ma sorge un problema: il firmware della stampante non permette l’utilizzo di due estrusori contemporaneamente, quindi per ogni movimento quindi rotatorio della stampante dovrò fare il cambio tool e fare un retract durante la stampa.
A questo punto l’ultimo problema rimasto è lo slicing, infatti non esiste un programma che calcoli anche i movimenti del nuovo asse.
Considerando che è stato inserito un solo nuovo asse, l’oggetto più interessante da stampare risulta il cilindro e modificare il gcode di un cilindro non è molto difficle sfruttando la geometria dell’oggetto.
Ho scritto uno script in python (non sono un informatico, quindi sono sicuro che ci sono modi più semplici o più efficienti per fare quello che ho fatto, vi prego non intasate i commenti con suggerimenti per lo script grazie=) ) che controlla riga per riga il gcode e va a calcolare l’angolo sul lato del cilindro in base alla variazione dell’asse x tra due layer e conoscendo il layer height.
Il resto del codice serve per inserire le righe del gcode che servono per gestire il movimento, considerando anche il punto di partenza dell’estrusore, il quale può essere su uno qualsiasi dei vertici del perimetro.
Risultati
Dai test preliminari risulta che la stampante utilizzata è già al limite delle sue potenzialità, infatti otteniamo dei risultati non molto precisi e puliti.
In ogni caso nelle seguenti foto si confrontano i due pezzi, in particolare si nota in alcuni punti un netto miglioramento rispetto ad una stampa senza rotazione.
A sinistra possiamo vedere come il pezzo risulti ben stampato rispetto all’immagine di destra dove si notano i filamenti che tendono a staccarsi.