Post introduttivo e indice.
Realizzazione della struttura del letto di stampa
Per realizzare questa struttura servono le seguenti parti:
1 Lastra in alluminio avente misure di almeno 210 x 210 x 4-5mm
8 Viti M4x25mm testa svasata + 8 dadi M4
4 viti M3x25mm testa svasata + 6 dadi M3 Nylonstop
2x viti M3x20mm testa svasata + 2 dadi M3
4 molle (non ho le specifiche esatte)
4 LM8UU Pillows
1 Y-BELT-HOLDER
Stampati in ABS con infill 80%
I files STL sono scaricabili qui (zip aggiornato): parti plastiche print_bed
Mi sono procurato la lastra in alluminio che verrà fissata sui 4 LM8UU pillows (aggiornati) e sulla quale verrà montato il print bed. Si tratta di un semilavorato in alluminio ricavato da un’apparecchiatura dismessa con dimensioni che fortunatamente sono di 240x244x5mm perciò adatte al mio scopo. Questo ripiano verrà trascinato dalla cinghia GT2 lungo l’asse Y. Su questo verrà fissato il print bed vero e proprio in plexiglass da 10mm tagliato al laser, fornito gentilmente dal fablab su mio disegno.
Per garantire un’area di stampa di 200x200mm ho dovuto calcolare una distanza di 80mm tra i cuscinetti LM8UU anteriori e posteriori dell’asse Y in base alla posizione Y esatta dell’ugello dell’extruder rispetto al piano di stampa che secondo il montaggio standard da manuale è 65mm.
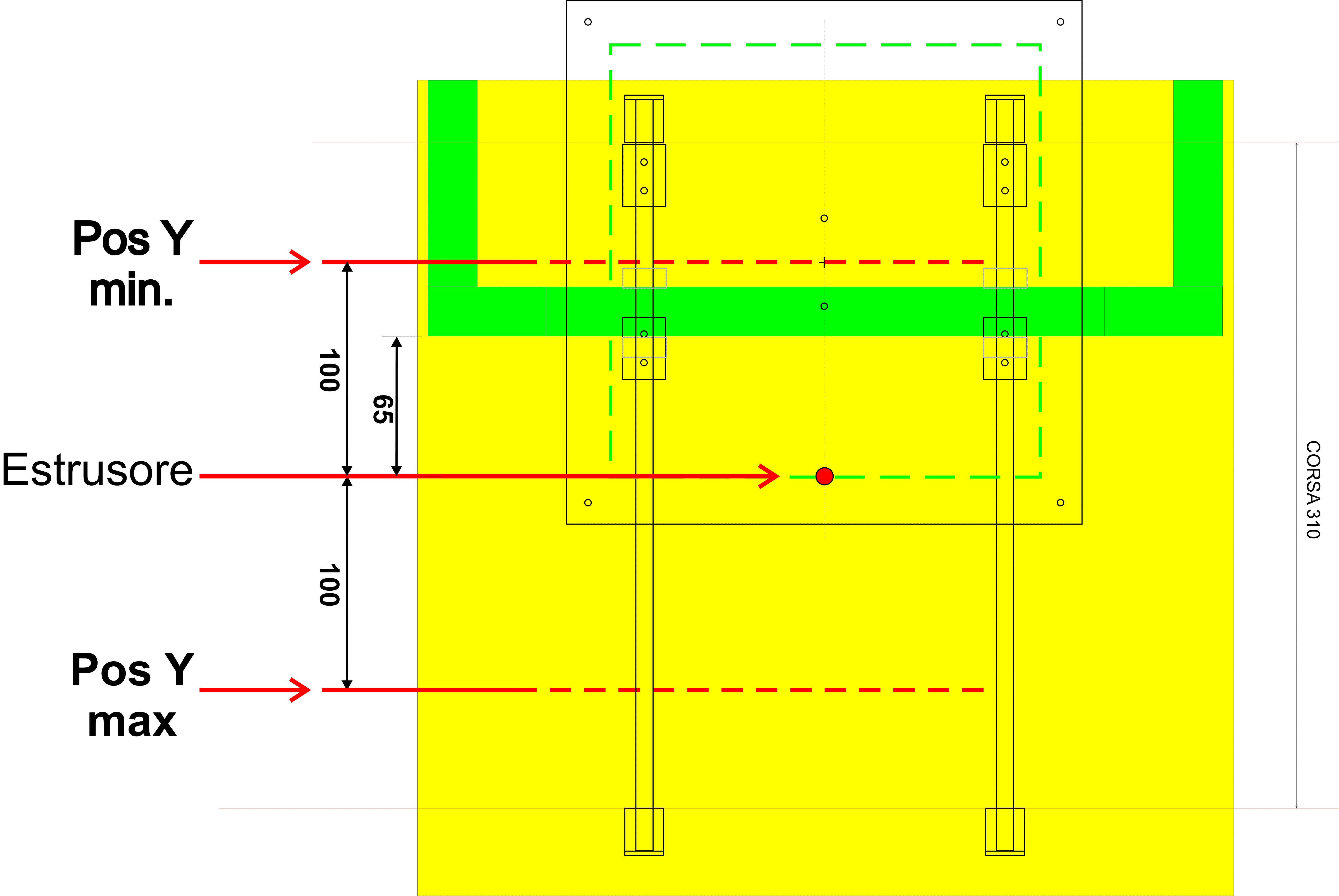
Presso il Fablab ho effettuato i fori in base al mio disegno BED_240x244_NEW
Nella la foratura della lastra di alluminio oltre ai 4 fori da 3mm agli angoli e i due fori verticali al centro, tenere in considerazione solo i fori da 4mm orizzontali per il fissaggio dell’LM8UU Pillow (supporto cuscinetti) e non quelli verticali da 3mm che servivano per i Pillows vecchio tipo.
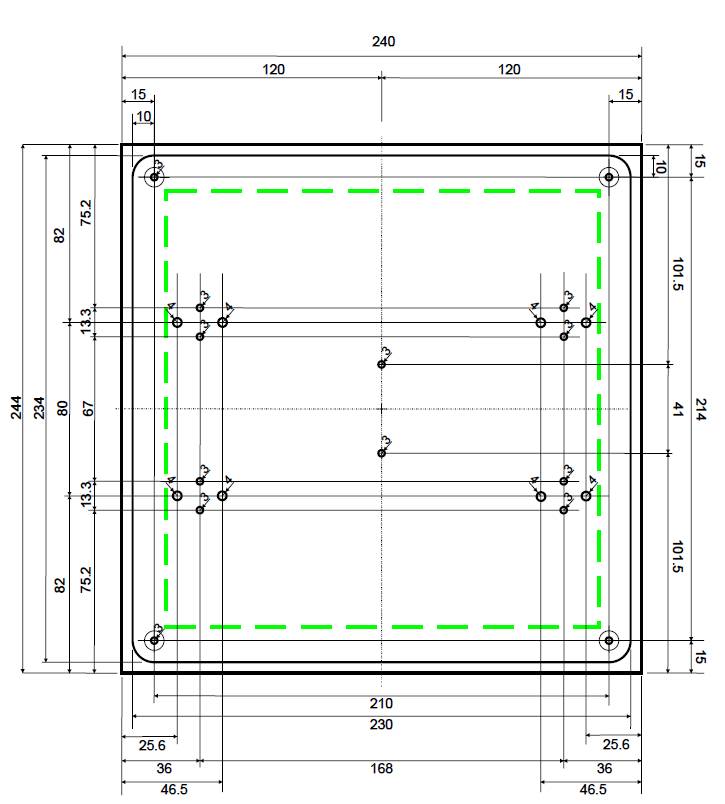
I 4 fori agli angoli serviranno per le viti M3x25 sulle quali saranno calettate le 4 molle sulle quali verrà appoggiato il piatto di stampa in plexiglass lasercut.
A cosa servono le molle?
Ora che lo so guai se mancassero!
Le molle servono principalmente per poter regolare l’altezza del letto di stampa in base al punto Z=0 raggiunto dall’estrusore.
La punta dell’estrusore deve sfiorare il letto di stampa (vedremo in seguito più accuratamente nella sezione Calibrazione) in tutti i punti. Per assicurarci questo, prima di tutto il letto deve essere assolutamente piano, e poi regolando le quattro viti poste ai 4 angoli del letto di stampa si tara questa condizione.
Esiste inoltre una ragione più effimera che promuove queste 4 molle che non devono essere troppo rigide in quanto devono poter essere schiacciate dall’estrusore quando l’asse Z fa il birichino…. All’inizio non ci credevo…. poi mi sono dovuto ricredere. Ogni tanto con smanettamenti estremi, annullamento di stampe ecc, l’asse Z scende sotto lo zero fregandosene del microswitch fracassandolo! Se non ci fossero state le molle sotto il letto di stampa, che mi hanno dato alcuni istanti di tempo per togliere l’alimentazione alla “bestia impazzita” avrei fracassato anche il corpo estrusore.
Gli stepper hanno una forza all’asse di 5Kg/cm! Non si fermano davanti a nulla!!
Lo dico ora e lo ripeterò anche in altri post: Quando si interrompe una stampa, premere subito dopo il pulsante di reset di Arduino per resettare tutta la stampante.
I 4 LM8UU pillows vanno inseriti a pressione sui cuscinetti lineari LM8UU .
Io ho usato una morsa per far entrare gradualmente il cuscinetto nel pillow.
Fare solo attenzione che il cuscinetto sia allineato in modo da entrare nello spazio a lui riservato nel pillow. Non usare martelli o maniere pesanti per questa operazione pena la rottura del pillow.
LM8UU pillow (nuova versione più robusta) Vanno a sostituire i precedenti LM8UU Pillows. Aggiornati anche nello zip scaricabile.
Inserire i dadi M4 negli appositi incassi esagonali dei supporti cuscinetto usando la punta del saldatore per inserirli a caldo evitando così di criccare la plastica.
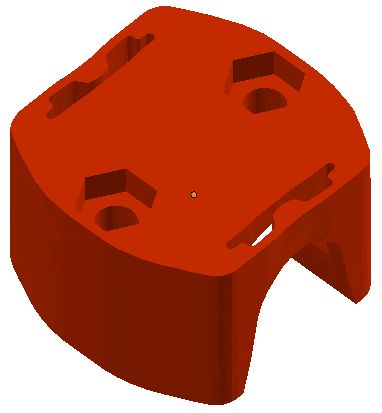
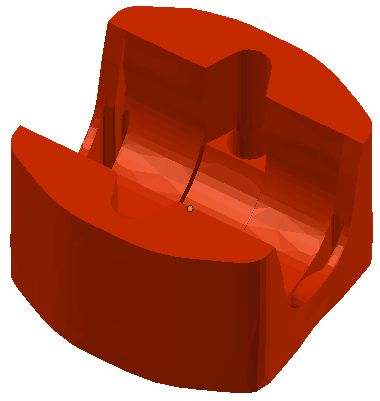
Particolare dell’assemblaggio Pillow – cuscinetto.
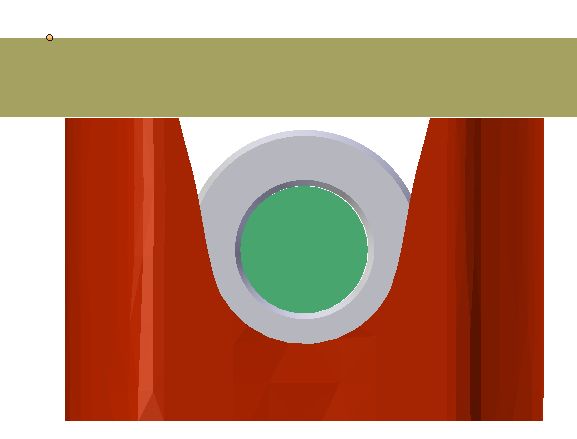
Usare le 8 viti M4x25mm per fissare i 4 LM8UU pillows alla lastra di alluminio. La lunghezza delle 8 viti va calibrata in funzione dello spessore della lastra di alluminio.
Se si usa un ripiano in alluminio di minor spessore, la lunghezza delle viti dovrà essere accorciata di conseguenza.
Se tra il bordo superiore del cuscinetto ed il bordo inferiore del ripiano di alluminio (vedi figura) dovesse esserci dell’aria, creare uno spessore abbastanza rigido di misura adeguata da introdurre durante il fissaggio per colmare questo gap. (io ho usato della gomma da camera d’aria)
Fissare l’ Y Belt Holder al piatto con le 2 viti M3x20 o 15mm.
Y Belt holder
Fissare poi la cinghia GT2 all’ Y Belt holder come indicato in figura e bloccare le estremità con una fascetta.
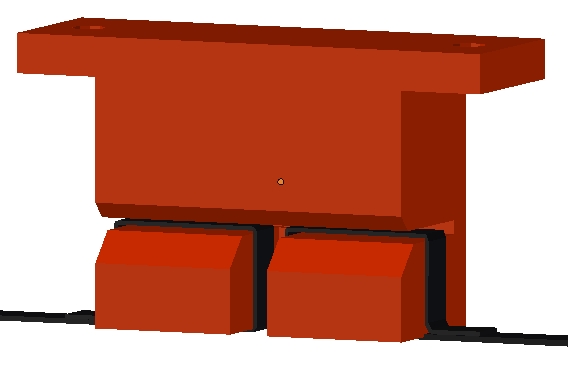
Per riassumere, l’esploso della struttura inferiore (I Pillows sono diversi).
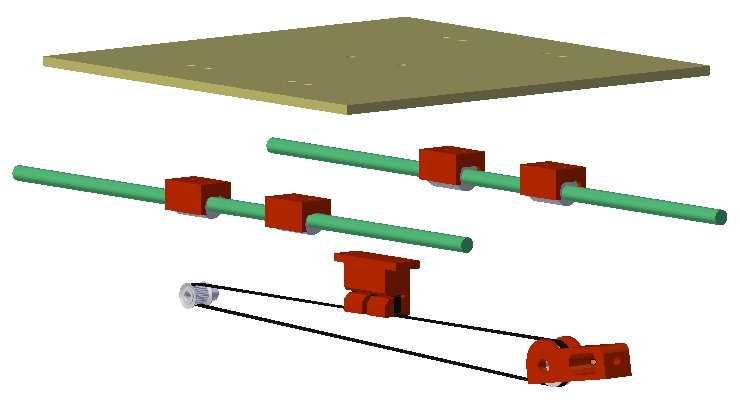
Andiamo ora a montare il letto di stampa vero e proprio sulla base in alluminio appena assemblata.
Questo è stato tagliato al laser presso il fablab utilizzando una macchina per taglio laser che si basa su un disegno dxf da me realizzato in base alle misure calcolate.
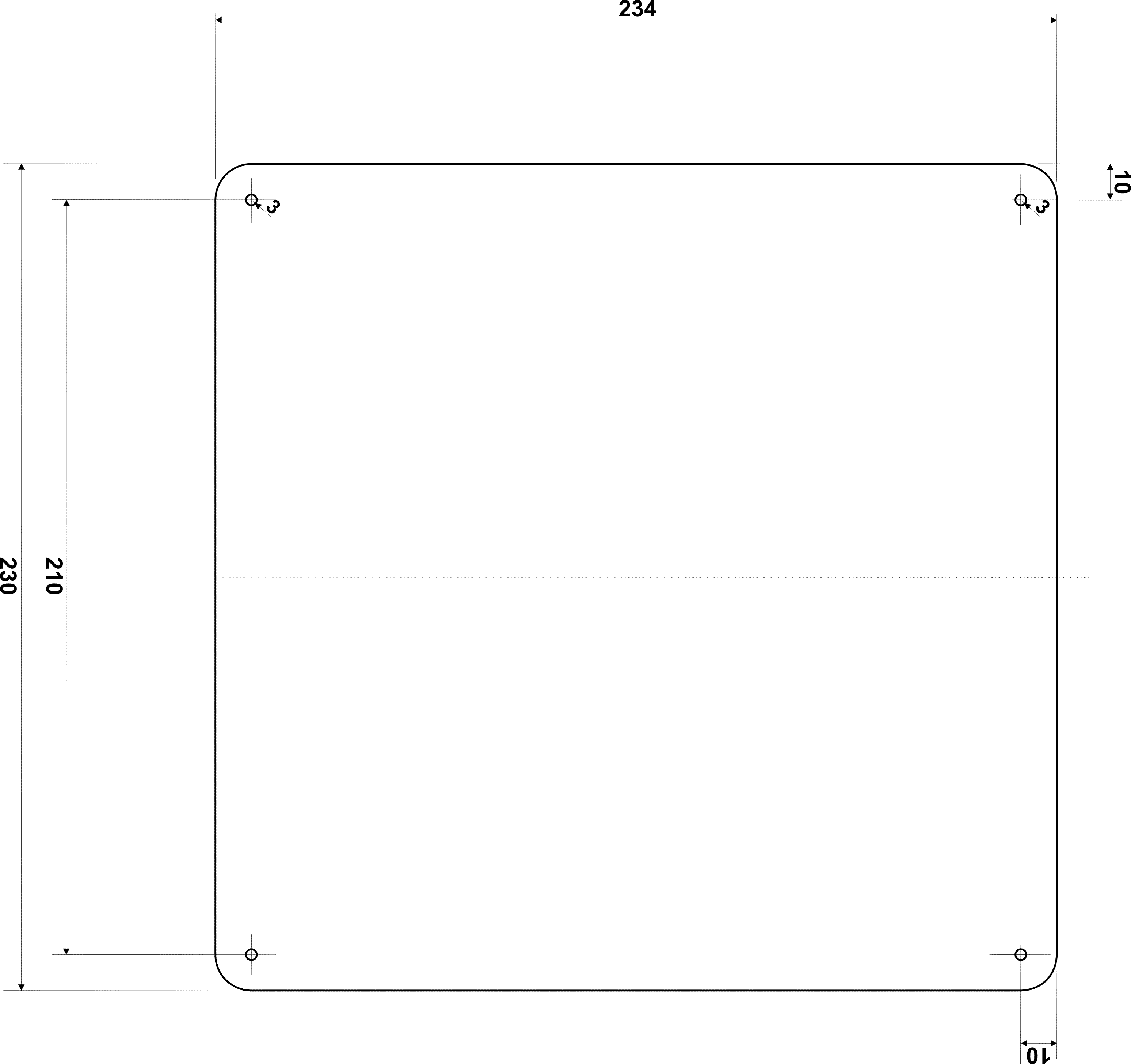
Il file dxf utilizzato si trova nel seguente zip: print-bed_230x234.zip
Le 4 viti M3x25 che sostengono il piatto di stampa in plexiglass mediante le relative molle, sono unicamente trattenute da un dado M3 nylonstop posto sotto il piatto di alluminio.
Questo rende facile la taratura del letto di stampa con l’ugello dell’estrusore ma presenta un inconveniente emerso solo dopo l’esecuzione delle prime stampe.
Nei movimenti bruschi (quasi sempre) il piatto di stampa in plexiglass, essendo piuttosto pesante, bascula per inerzia di circa +/- 0.5mm in direzione Y a causa delle viti che non sono fissate saldamente a piano inferiore. Questo non fissaggio causa anche un continuo e sgradevole scricchiolio durante la stampa.
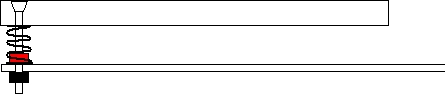
Per fare in modo che la vite su cui scorre verticalmente il piatto di stampa grazie alla molla, non oscilli lungo l’asse Y durante i movimenti del piatto, ho inserito un secondo dado nylonstop M3, sopra il ripiano in alluminio (indicato in rosso in figura).
E’ stato sufficiente aggiungere questo dado solo alle viti anteriori del piatto di stampa per dare maggiore rigidità orizzontale in asse Y a tutta la struttura.
L’eventuale taratura del letto di stampa potrebbe essere un tantino più complessa ma i risultati ci sono.
Questa modifica ha annullato il wobble (discontinuità dell’estruso in direzione Y) riscontrato sui pezzi fin’ora stampati.
Fissaggio della struttura Y al telaio della stampante.
Terminato l’assemblaggio della struttura metallica dell’asse Y con il letto di stampa, io ho verniciato il telaio in legno previa stuccatura delle parti ruvide (parti tagliate ecc.).
Per la verniciatura ho usato un nero opaco da carrozzeria antigraffio in bomboletta
In foto si può notare il nuovo look del frame appena stuccato e pitturato con il piano di stampa fissato con le viti e le molle di livellamento.
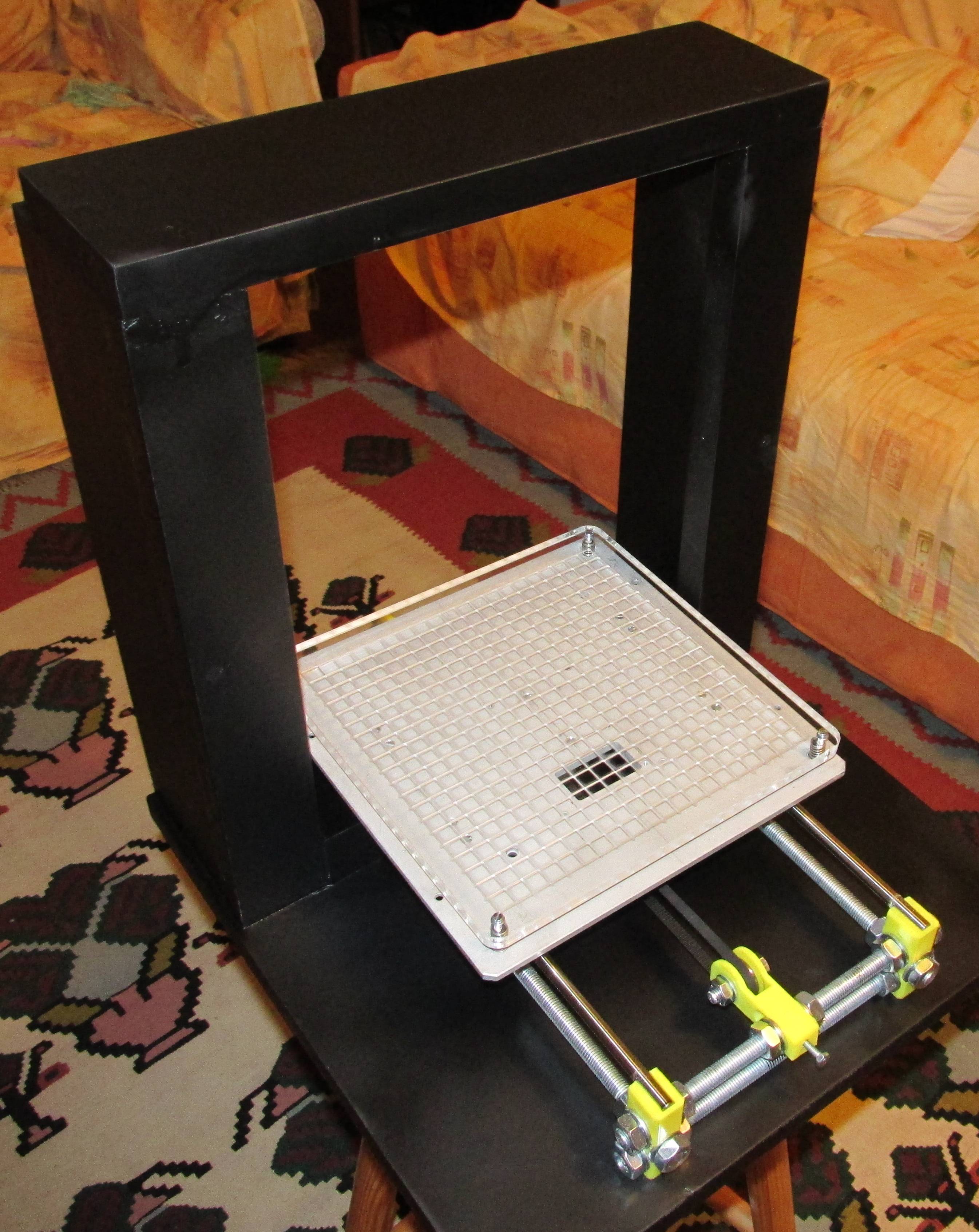
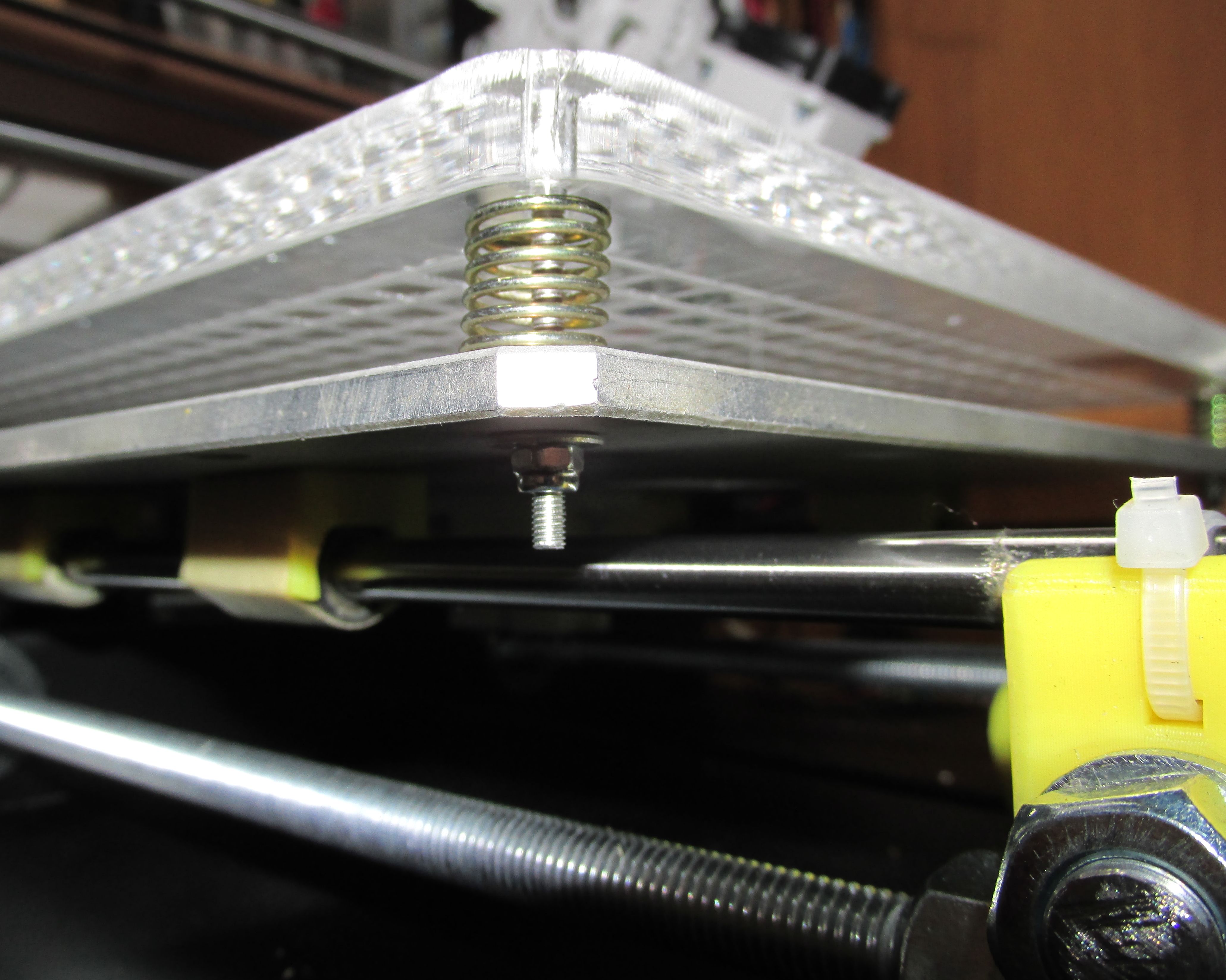
Ora si deve fissare tutta la struttura al telaio della stampante.
Prima di tutto si devono regolare i dadi M10 e relative rondelle da 39mm inseriti precedentemente nelle barre filettate M10 longitudinali da 380mm dell’asse Y ad una distanza di 245mm dal corner anteriore (vedi figura).

Precisamente i dadi M10 anteriori e rondelle anteriori vanno avvitati alla distanza indicata mentre i dadi e rondelle posteriori saranno di conseguenza 20-25mm più in dietro (dipende dallo spessore del tramezzo in truciolare)
Questa regolazione va poi verificata con estrusore montato per centrare l’escursione Y con il letto di stampa in base alla posizione dell’ugelllo di stampa.
Effettuate queste regolazioni è possibile stringere i 4 dadi M10 sulle asole del tramezzo.
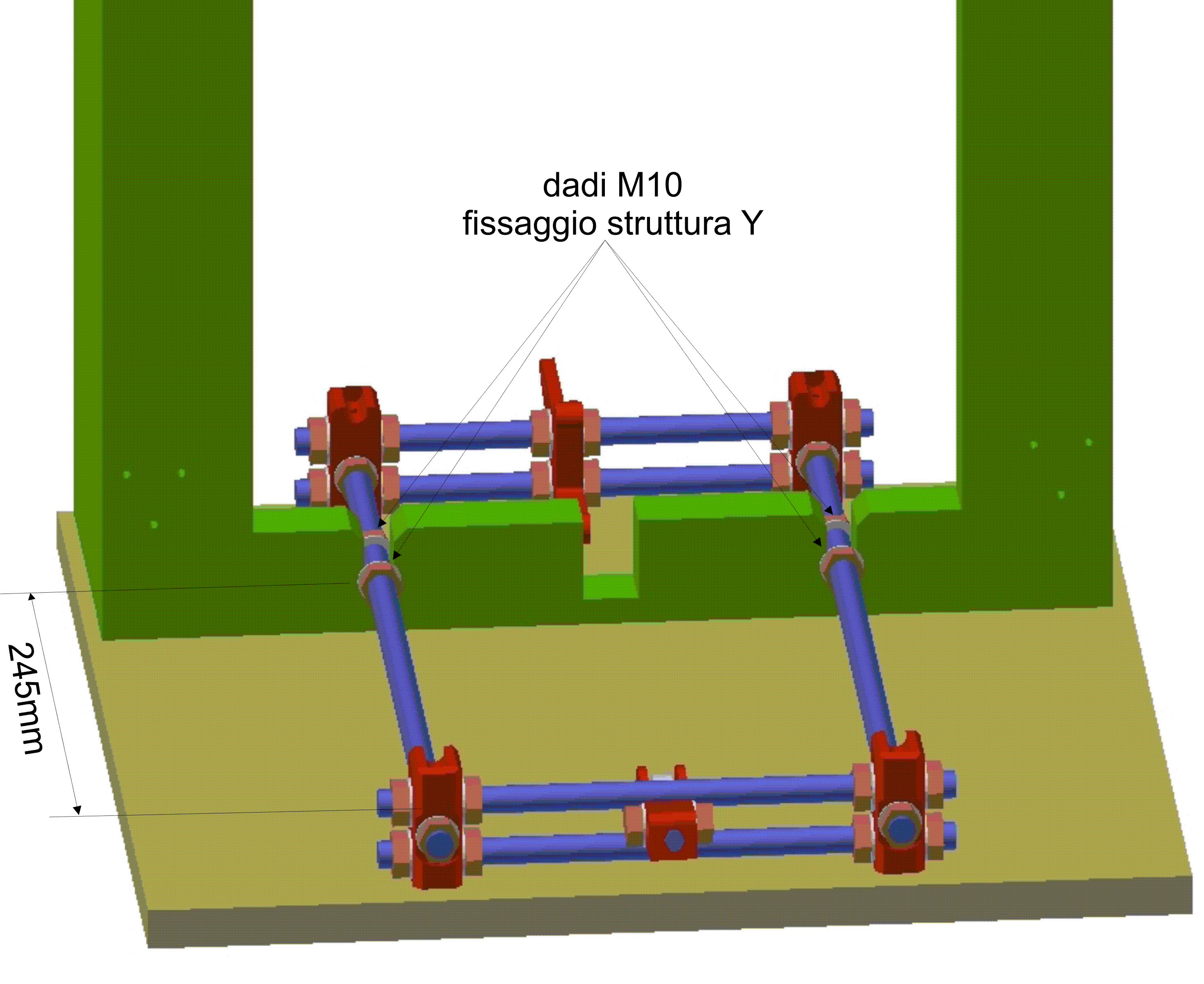
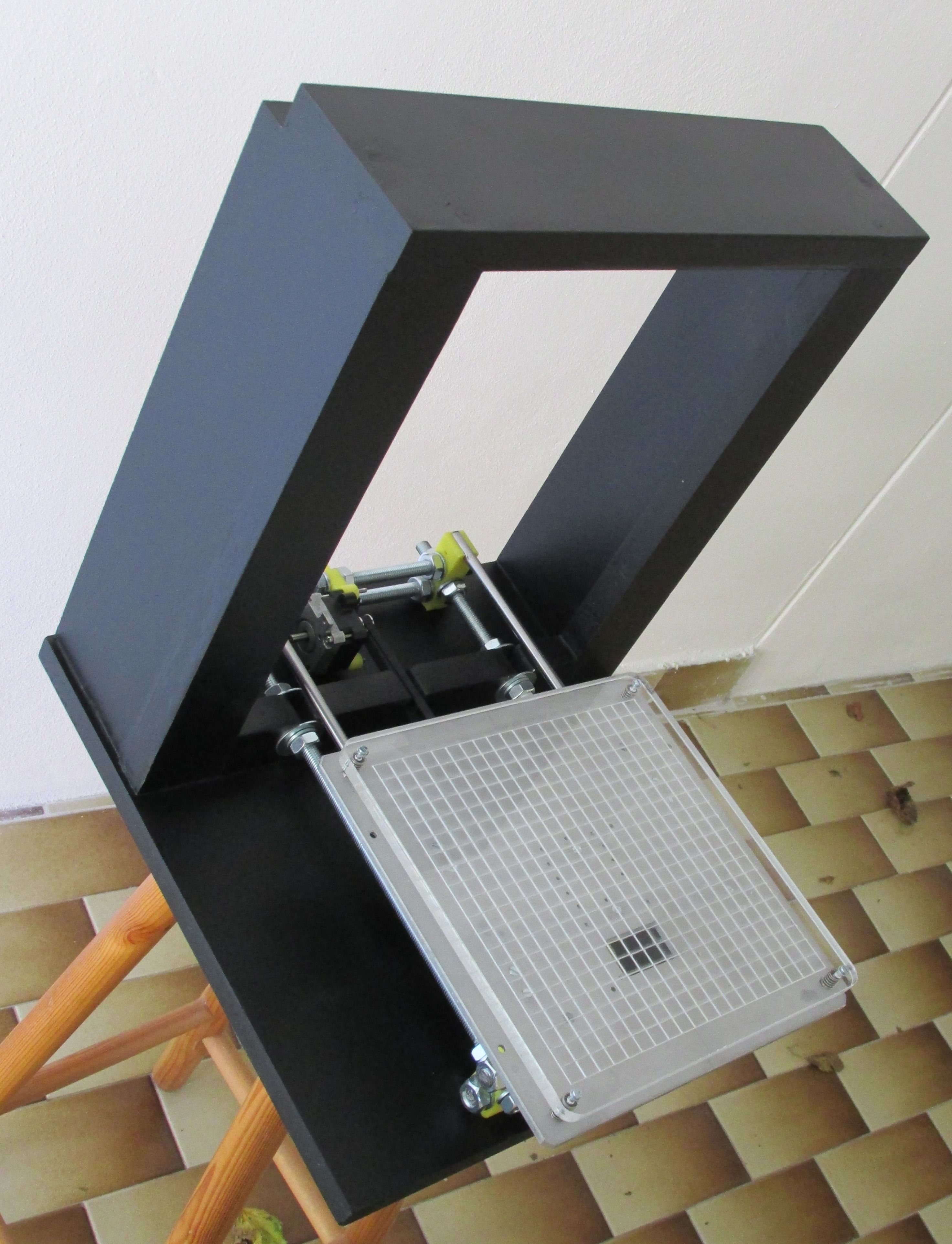
Questo il risultato prima della regolazione finale.
Post successivo: I motori Stepper per la Prusa i3
Post introduttivo e indice.